Modern manufacturers deal with intensely complex supply chains and shop floors. Faced with rising consumer expectations for quality, speed, and flexibility, production teams often struggle to deliver. Messy, disjointed processes are common – creating bottlenecks that slow down operations and cap output. However, exciting cloud-based applications are set to transform age-old production management approaches with new efficiency. This post explores the top 5 cloud apps that manufacturers urgently need to embrace.
Table of Contents
The 5 Killer Cloud Apps Upgrading Production Management
1. IoT Analytics: Cutting-Edge Predictive Maintenance
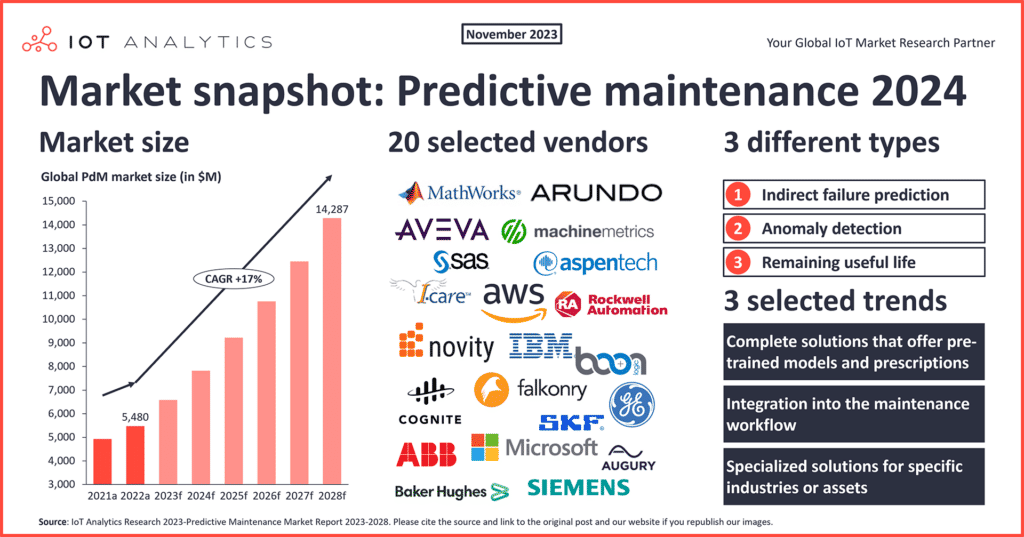
Source: https://iot-analytics.com/predictive-maintenance-market/
Industrial IoT platforms tap into sensors across factory equipment and machines, collecting performance data to feed powerful cloud-based analytics. By applying AI to discern insights not visible to the human eye, these tools enable predictive maintenance.
For example, algorithms track vibration frequencies in motors to detect subtle early changes indicative of failures weeks before occurring. Teams can then preemptively service equipment, slashing downtime versus reactive fixes after costly breakdowns. Intel estimates manufacturers can achieve over 10% production output increases through IoT-powered maintenance alone.
McKinsey research found that smart factories able to forecast issues through IoT analytics average:
- 20% reduction in machine downtime
- 25% decrease in maintenance costs
- 75% fewer breakdown-related accidents
As IoT and AI illuminate emerging risks early, teams prevent prolonged outages. By keeping machines humming 24/7, output stays consistent.
2. Inventory Optimization: Balancing Orders and Output
Disjointed inventory tracking often leaves teams guessing on optimal stock levels. But AI-powered inventory optimization software like Brightpearl and TradeGecko applies predictive algorithms to forecast demand shifts. By tapping historical ordering volumes, sales trends, and emerging signals, these tools derive ideal levels tailored to future needs.
Automated dashboards also provide real-time visibility so managers understand what products are overstocked versus constrained. This allows dynamically shifting production queues based on inventory health, keeping output aligned with true demand. Through AI-optimized planning, manufacturers can achieve over 20% working capital improvements.
3. Digital Twin Apps: Simulating Smarter Factories
Digital twins are virtual replicas of factories. By simulating plant layouts and workflows within physics-driven 3D software, teams can thoroughly test endless configuration options digitally before costly physical implementations. Models reveal how floorplan adjustments, machine footprints, conveyor paths, and more impact overall efficiency.
Stellantis, the automotive manufacturer, uses digital twins to create “virtual build events”. These predictively identify bottlenecks in vehicle assembly sequences before launch by modeling thousands of permutations. Such insights then optimize actual factory and robot positioning for smoother flows. Accenture estimates over 10% throughput gains using this approach.
4. AR-Powered Workflow Apps: Intuitive Shop Floor Assistance
Many employees still rely on outdated paper guidelines full of complex workflows. This strains productivity and quality. AR-powered workflow apps like Atheer overlay step-by-step guidance directly in workers’ fields of vision via smart glasses. Contextual instructions guide each phase, freeing hands for tasks while reducing mistakes. Workers can also share live video feeds for remote troubleshooting help.
Studies by companies like Boeing and GE showed AR assistance can accelerate production tasks by over 30% versus traditional methods. As more hands-free tools enter shop floors, teams gain an always-available assistant guiding them through even the most intricate assemblies based on real-time needs.
5. Centralized Production Dashboards: Data Consolidation Driving Decisions
While managers once monitored metrics in siloed sources, cloud-based analytics consolidate all data into unified views. Platforms like CloudSense and Sight Machine intake inputs from across operations – from inventory levels to quality yields and machine performance. This single pane of glass enables proactively identifying crucial emerging trends.
As outputs waver or orders surge, decisions can shift queues and staffing accordingly. Removing data blindspots enables tightly aligning production to consumer demand. According to Gartner, analytics-optimized manufacturers show on average 9% higher productivity gains than peers.
Conclusion
The 5 cloud-based applications highlighted above showcase how emerging technologies can transform outdated production management approaches. As innovations in IoT, predictive analytics, digital twin modeling, AR guidance, and consolidated data offer new solutions, manufacturers can optimize efficiency, output, and processes like never before. By leveraging the cloud to introduce cutting-edge apps into legacy workflows, both large enterprises and small factories can future-proof operations.
FAQs
Leading cloud platforms utilize top-tier security like 256-bit SSL encryption for data in transit and at rest, strict access controls, VPC services, and advanced threat detection. They also comply with standards like SOC2 and ISO 27001 with independent audits. Multi-factor authentication prevents unauthorized access.
Lightweight cloud apps can be rolled out in as little as 2-4 weeks. More complex system integrations connecting legacy programs can take 6-8 weeks when factoring data migration, testing, and user training. Gradual phase-in options can accelerate timelines as well.
Based on case studies across industrial manufacturers, teams can expect:
10-20% equipment effectiveness gains
15-30% increased production throughput
25-40% reduced unplanned downtime
8-15% labor efficiency improvement
10-20% cost savings over inventory and maintenance